Dynamic lineside replenishment: a strategic response to today’s manufacturing challenges
Julkaistu 15. heinäkuuta 2024: Flexible Manufacturing
It’s time for a rethink on lineside replenishment systems and practices, if manufacturers are to remain efficient and competitive whilst meeting the challenges posed by customisation and labour shortages. Could AMRs and cobots be the answer?
The customisation trend has created numerous operational challenges for manufacturers; the need to accommodate a wider array of components and materials introduces variability that traditional systems struggle to manage efficiently. This can lead to increased inventory costs, longer lead times and production delays.
Empirical data underscores the impact of customisation on manufacturing operations; manufacturers reported to have faced extended lead times, higher production costs, and the need to manage multiple inventories. These figures illustrate the tangible challenges that customisation poses, necessitating innovative approaches to manage this complexity efficiently.
Lineside replenishment: a pain point
Lineside replenishment, which includes tasks such as just-in-time (JIT) delivery of consumables and optimising the transport of goods, boxes and pallets, is one area that becomes particularly challenging with greater customisation. The acute labour shortage facing the manufacturing industry isn’t helping this situation, as many lineside replenishment tasks are traditionally manually intensive. With fewer workers available to move materials to and from production lines and to manage inventory, manufacturers must seek more efficient and less labour-dependent solutions.
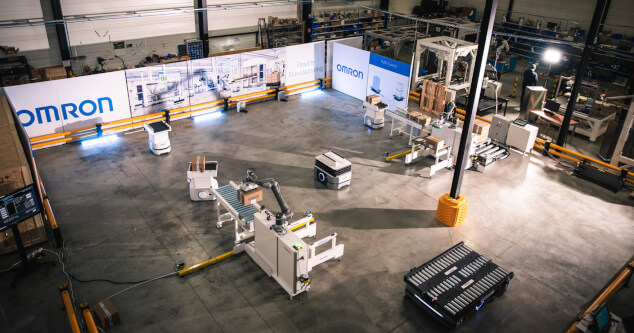
How it looks in the pharmaceutical industry
In the pharmaceutical manufacturing sector, for example, a critical bottleneck has emerged in the physical transportation of clean, empty vials and secondary packaging materials to production lines primarily due to a lack of available workforce to push carts. This challenge is even more marked in environments where forklifts and other mechanical handling equipment are not viable due to the strict hygiene standards and spatial constraints typical of pharmaceutical facilities. With a shortage of personnel available to transport materials, this has led to delays in the production process, so the timely and efficient supply of these essential components to the production line is disrupted.
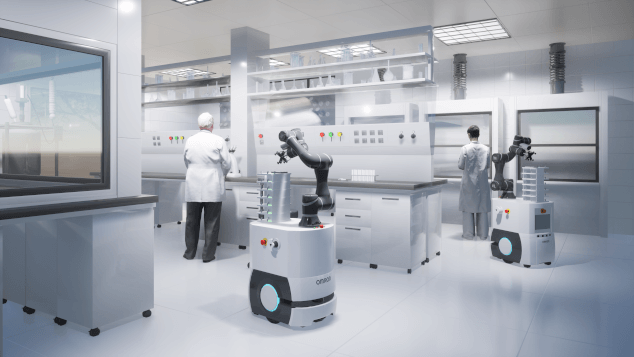
Automated lineside replenishment solutions
Addressing these inter-connected challenges calls for a holistic approach that leverages technology and innovation. In this respect AMRs (Automated Mobile Robots) and cobots offer a promising solution. These emerging technologies are capable of reducing the labour intensity of lineside replenishment and accommodating the variability inherent in customised production.
Here are just some of the advantages of adopting these robotic technologies:
- On-demand consumables: AMRs can be programmed to deliver materials precisely when and where they are needed, minimising unnecessary inventory on the production floor and reducing the physical strain on workers. For example, deploying AMRs for the delivery of packaging materials or work in progress (WIP) enables continuous production, accommodating variability in Stock Keeping Units (SKUs) without disruption.
- Flexibility and scalability: in comparison with traditional conveyor systems, AMRs are dynamic. They can be integrated seamlessly with Manufacturing Execution Systems (MES) and are scalable up to 100 robots or more. This flexibility makes them particularly suited to environments where product specifications frequently change, ensuring that manufacturers can adapt quickly to customisation demands without compromising efficiency or safety.
- No margin for error needed: the precision with which AMRs deliver consumables and WIP to production lines minimises the risk of errors. This accuracy is crucial in maintaining high productivity levels and operational efficiency; by ensuring the right materials are always at hand when needed, they eliminate unnecessary delays and improve overall process flow.
- Predictive replenishment: advanced automated systems are not only reactive but also proactive, capable of monitoring consumption rates and predicting when materials will be depleted. This predictive capability ensures that replenishments are executed seamlessly, eliminating the potential for stoppages due to material shortages.
- Worker safety: AMRs also address one of the most common concerns associated with automating lineside replenishment tasks: worker safety. Traditional robots require extensive safety measures to prevent obstacles, whereas AMRs and cobots are designed to operate in harmony with human workers.
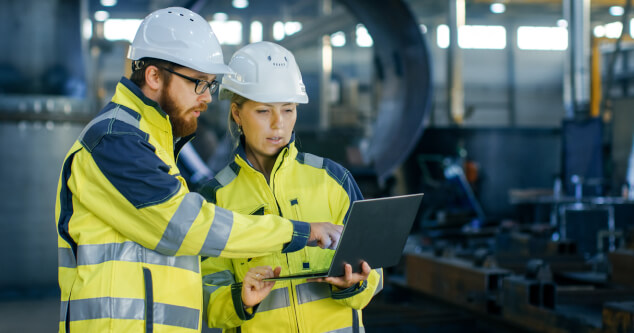
AMRs: a research-backed approach
Research in the field of advanced manufacturing underscores the efficacy of integrating AMRs into the production environment. Boston Consulting Group reports that the implementation of AMRs in a manufacturing setting can reduce in-plant logistics and warehousing costs by approximately 30%.
Embracing a new era of efficiency
In conclusion, customised manufacturing and the labour crisis have created a perfect storm for heightened pressure on lineside replenishment. The integration of AMRs for delivery and cobots for material feeding has the potential to revolutionise how materials - from consumables to WIP - are managed, giving manufacturers access to a new paradigm of production efficiency. By ensuring timely, accurate, and efficient line replenishment, these robotic fleets, when managed with precision fleet management techniques, can address bottlenecks stemming from labour shortages and customisation demands.
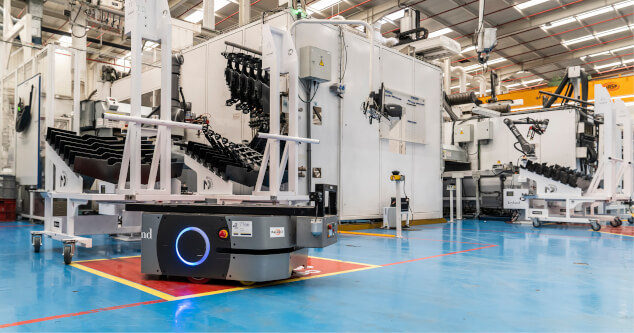