Vadain automates the inspection of curtain fabrics with machine vision
Julkaistu 08. huhtikuuta 2022: Brand Protection
The challenge: Flawless curtains
Delivering flawless curtains is a top priority for Vadain. In addition to the right dimensions, correct production method and finishing, identifying and preventing fabric defects before they enter production is a crucial step. If any flaws are detected once the curtains are hung at the customer’s premises, they are very costly to remedy, including replacing the product, as well as all associated logistics processes and work hours.
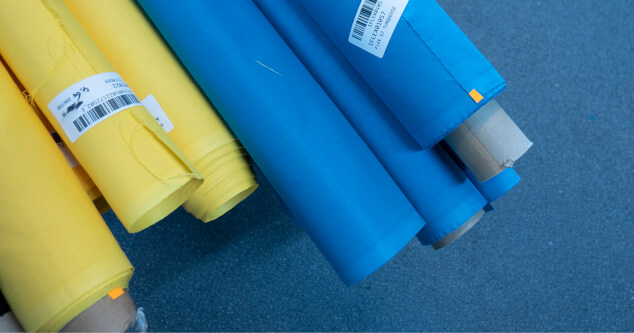
Production defects
As a rule of thumb, Vadain estimates that an average roll of fabric may contain a maximum of 5 defects, such as weaving errors or stains. In the best case, a fabric supplier has already marked the flaws in the roll. However, the responsibility for detecting and processing the defects is passed on to Vadain.Quality checks
To prevent any defects, several checks are made between the receipt of goods and dispatching the finished product. The first check takes place when the material arrives and is stored in the warehouse. More checks are carried out prior to production and at the workshop before production, as well as a final quality check of the finished product before shipment. The inspection was done manually, by unrolling and rolling the fabric over light boxes.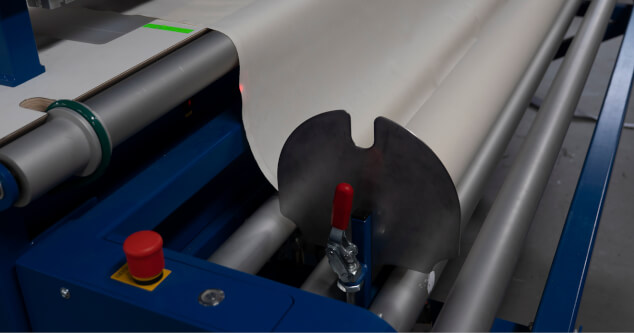
Solution with machine vision
The team at Vadain thought that there must be a better, more efficient and faster way to inspect the fabrics, and presented the challenge to Sycade, an expert in the field of quality improvement through automation in the manufacturing industry. Sycade proposed a concept to automate the inspection process with a machine vision solution. The solution performs checks faster and more accurately, reduces complaints and cutting loss* and ultimately results in cost savings. With the expertise of Vadain, the technology and innovative automation concept of OMRON, hardware of Eisenkolb and a camera light supplier, Sycade set up a solution using a 'standard' rolling machine to unroll rolls from position A and roll up again to position B. The unrolled fabric passes over an assessment surface with an integrated cutting unit, located inside a dark unit with vision technology.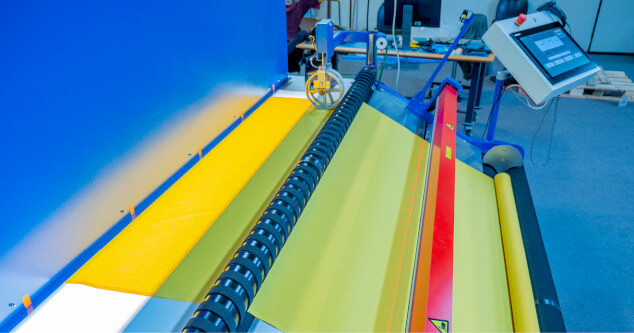
Cutting loss*
Cutting loss occurs when rolls are cut for production. Residual pieces are regarded as cutting loss, and largely disposed of as waste. By accurately documenting fabric lengths on partial rolls—and matching these with the requirements for each order—cutting loss, waste and the associated costs can be minimized.
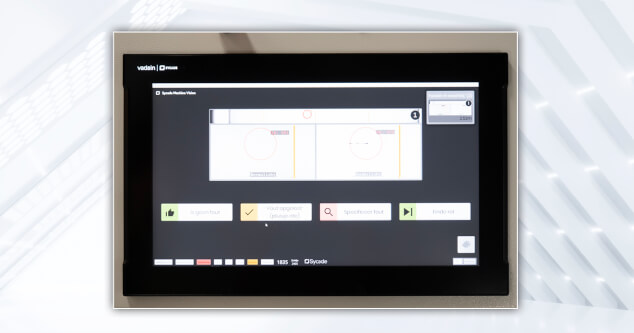
Intelligent software
The lighting and camera inspection system can detect even the smallest deviations in substances, thanks to intelligent custom software from Sycade and 'customized' standard hardware from OMRON. However, it is not enough to simply find a fault in a roll of fabric. Fabrics are not all equally thick or transparent, and they come with different weave structures, colors and reflection. The correct light and camera adjustments and programming settings were discovered after a series of tests.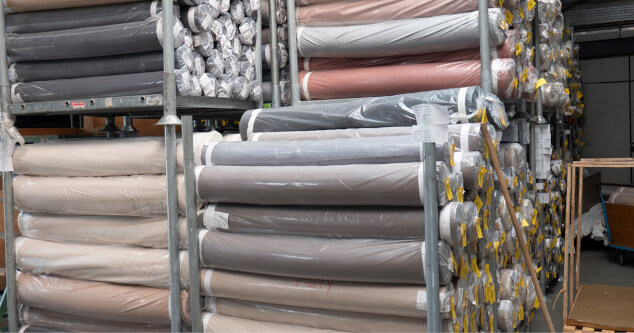
Detect, cut, register
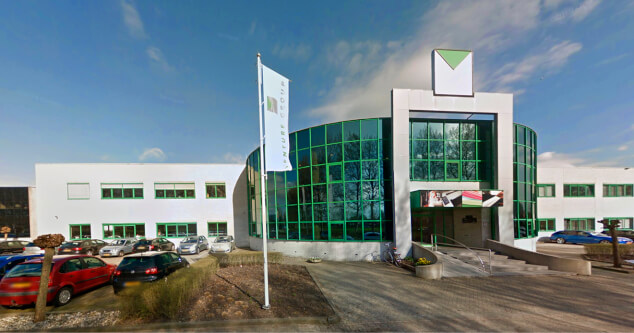