Integrated data control, motion control and machine vision for next-generation automotive production line
Julkaistu 24. huhtikuuta 2020: Industry 4.0
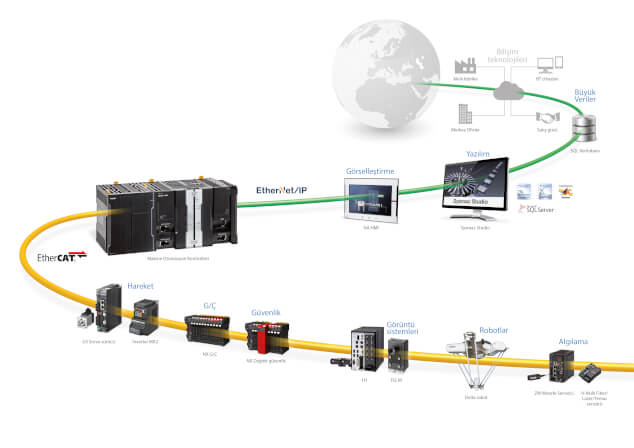
Meillä on teknisiä ongelmia. Emme ole pystyneet vastaanottamaan lomakettasi. Pahoittelemme ja pyydämme yrittämään uudelleen myöhemmin.
DownloadMeillä on teknisiä ongelmia. Emme ole pystyneet vastaanottamaan lomakettasi. Pahoittelemme ja pyydämme yrittämään uudelleen myöhemmin.
DownloadFill in your details below and get direct access to content on this page
Meillä on teknisiä ongelmia. Emme ole pystyneet vastaanottamaan lomakettasi. Pahoittelemme ja pyydämme yrittämään uudelleen myöhemmin.
DownloadYou now have access to Integrated data control, motion control and machine vision for next-generation automotive production line
A confirmation email has been sent to
Continue to pagePlease log in or get direct access to download this document
Julkaistu 24. huhtikuuta 2020: Industry 4.0